The eight common problems when using glass fiber reinforced PP flame retardants are as follows: 1. Why does the intumescent halogen-free flame retardant lose its flame retardant effect after adding filler or other substances?
In order to reduce the cost, many manufacturers added some fillers such as talc powder, calcium carbonate, barium sulfate, etc. to the PN-based intumescent halogen-free flame retardant, and found that the flame retardant effect was lost. Because the addition of the above filler changes the esterification reaction process, the acid source partially reacts with the above filler, and the above filler destroys the formation of the carbon layer on the surface of the material, resulting in failure of the mechanism.
2. Why does the effect of the intumescent halogen-free flame retardant on glass fiber PP deteriorate?
Since the addition of glass fiber destroys the flame-retardant mechanism of the PN expansion system, the glass fiber is distributed in various places of the plastic, which has a great destructive effect on the closure of the carbon layer, so that the oxygen can not be insulated to achieve the flame retardant effect.
3. Why do some PPs produced with PN-based flame retardants settle after a period of time (several days) with oil or powder on the surface?
The composition of the flame retardant we mentioned consists of a carbon source, an acid source and a gas source, causing the precipitation of substances into one or more of the above substances, and the compatibility with plastics is deteriorated. The material and the above powder are dispersed by the strong mechanical force of the screw machine, and after being left for a period of time, due to the continuous movement between the molecules, the substances with different polarities are slowly separated, and the powder is slowly taken from the material. The interior is deposited to the surface.
4. Why do some PN series flame retardants show foaming or graying when PP is processed?
Any flame retardant has its initial decomposition temperature, which is likely to occur if the decomposition temperature of the flame retardant itself is only close to the melting temperature of the material. Therefore, in general, the initial decomposition temperature of the flame retardant is at least 50 degrees higher than the temperature of the plasticizing process of the material, so as to ensure smooth processing.
5. Why do some PN-based flame retardants stick to water when they are squeezed through the sink?
The sliver is easy to stick to water because the water-soluble component of the flame retardant is relatively good. When passing through the outlet of the screw machine, the sliver with a relatively high temperature comes into contact with the cold water tank, and the powder is easily precipitated. Therefore, the composition of the flame retardant must be Water is insoluble.
6. Why do different PPs add the same number of flame retardants to the difference in flame retardant efficiency?
The difference of PP matrix, such as homopolymer PP or copolymerized PP, due to the difference of internal ethylene content, the flame retardant is different. In general, the copolymerization of PP is more difficult than the flame retardation of homopolymer PP. The fuel may also be more.
7. It is often seen that someone directly tests the extruded spline with a lighter to judge the flame retardancy of the material. It has certain rationality and certain limitations. Why?
The flame retardant test is carried out directly on the product with a lighter. For the halogen system, it is easier to judge, because the mechanism of the system determines that the degree of compaction of the product has little effect on the flame retardant effect, as well as the hydroxide system; but for the nitrogen and phosphorus system Carbon-forming flame retardant, due to the carbon-forming mechanism, the degree of compaction of the product has a relatively large effect on the flame retardant. For example, the strips that have just been extruded have a limited degree of compactness, and there may be some pores inside, which have side effects on char formation, and after injection molding. The compactness of the products is greatly enhanced, and the charcoal effect is also more rapid.
8. When using nitrogen-phosphorus intumescent flame retardant to flame-retard PP, and achieve UL 94V-0 flame retardant level, can it reduce the flame retardant level to UL 94V by reducing the amount of nitrogen-phosphorus intumescent flame retardant added? 2, thereby reducing costs?
No. Since the flame retardant mechanism of the nitrogen-phosphorus intumescent flame retardant is "carbon forming" and "foaming", the effects of heat insulation, oxygen inhibition and flame retardancy are achieved. Therefore, reducing the amount of the nitrogen-phosphorus intumescent flame retardant added does not form a complete char-forming or foaming layer, and thus does not provide a flame retarding effect.
Abrasive Sanding Disc
Due to its wide range of uses, there are also many varieties of hook and loop sanding disc. The most commonly used are red sanding disc, yellow/gold sanding disc, green sanding disc, and white sanding disc, etc.
The sandpaper disc is using aluminum oxid abrasives, with grits as below: 40#, 60#, 80#, 120#, 180#, 240#, 320#, 400#, 600#, 800#, 1000#, 1200#, 1500#, 2000#.
The abrasive polishing disc can be punched into various shapes, round, round with holes, triangle, rectangle, iron shape, neckline shape, etc.
This product is round abrasive disc size: 100mm, 125mm, 150mm, 180mm, 225mm or other size can be customized.
The holes best selling is with 6 hole, 8 holes, 15 holes, 17 holes or customized.
The main purpose of our abrasive sanding disc:
1. Polishing of primer and finishing of paint, such as mid-coat paint/primer grinding of ships.
2. Polishing of synthetic materials, such as burr sharp edges and surface adjustment after plastic products are formed.
3. Grinding of metal and aluminum alloy to remove foreign matter and surface particles.
4. Suitable for making various specifications of brushed and self-adhesive sand discs.
This abrasive sanding disc is one of our main abrasive products, as the manufacture of abrasive tools, we mainly produce the Flap Disc Backing Pad, Flap Disc Adhesive, Abrasive Flap Disc, bonded abrasives( Cutting Wheels and Grinding Wheels ), Abrasive Machine , etc. So welcome more orders, we can offer you best quality product with best competitive price, please contact Emma.
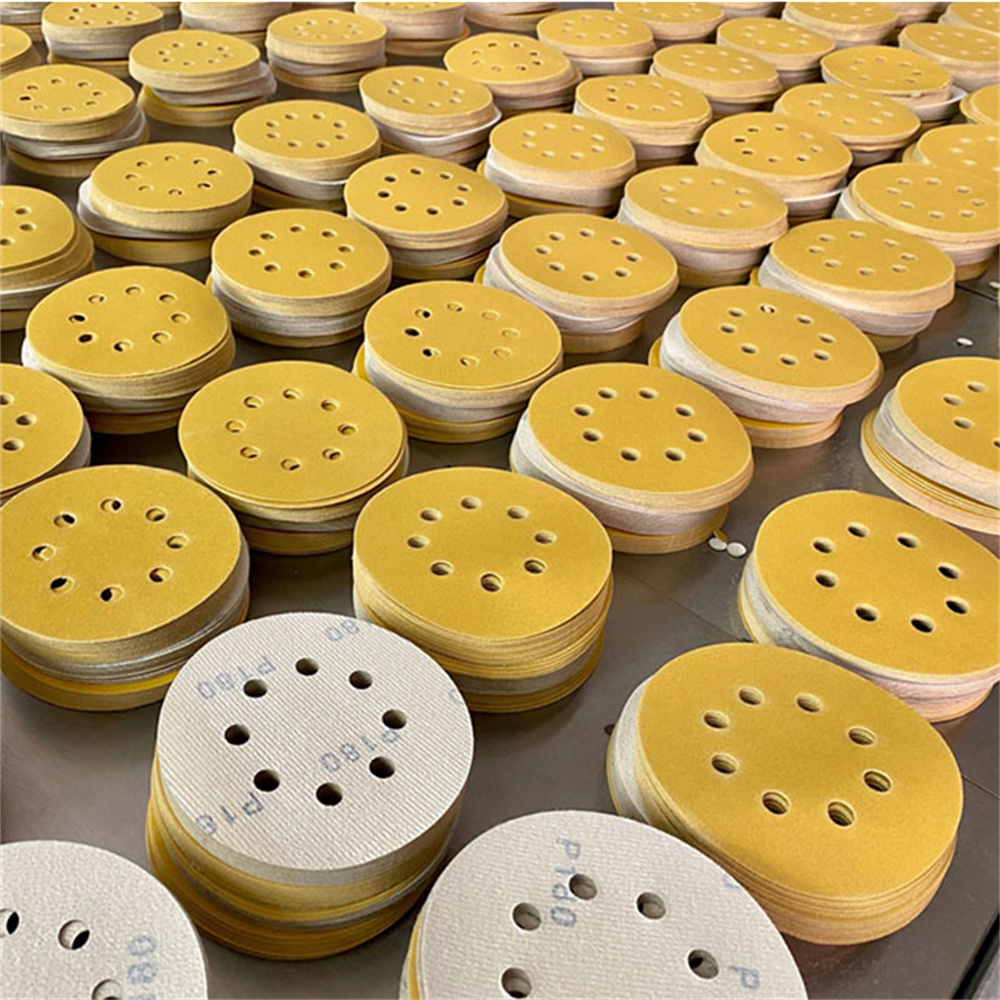
Abrasive Sanding Disc,Sanding Disc,Metal Sanding Disc,Abrasive Tools Sanding Disc
Zhengzhou Jiading Abrasive Manufacturing Co.,Ltd , https://www.jd-abrasives.com